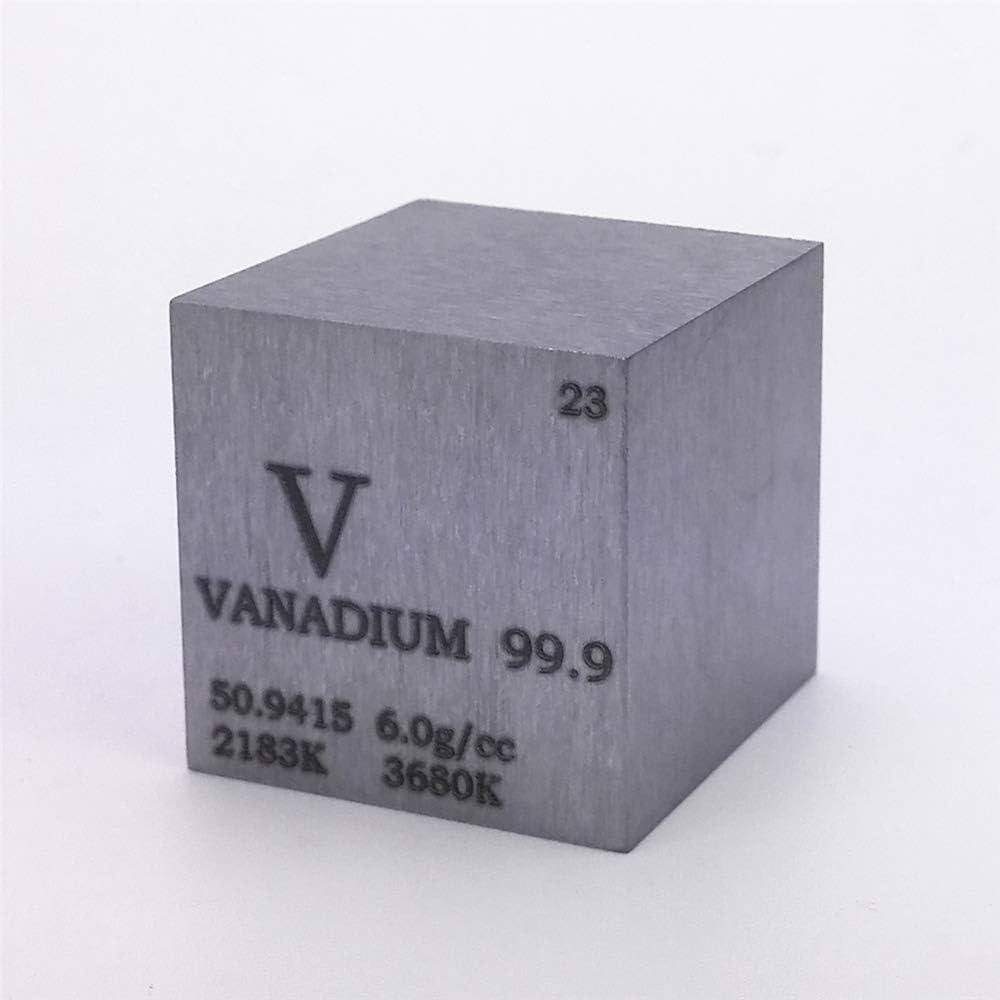
Navigating Vanadium (V)
Scientific Properties of Vanadium
Vanadium is a hard, silvery-grey transition metal with atomic number 23 and symbol V. It has a high melting point of 1,910°C and is primarily found in minerals such as vanadinite, patronite, and carnotite. Vanadium forms compounds in multiple oxidation states and is used as an alloying element to improve the strength, toughness, and heat resistance of steels. It also finds applications in aerospace alloys, catalysts, and energy storage systems.
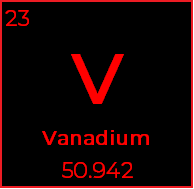
Uses and Future Applications
The primary use of vanadium is in the steel industry, where it serves as an alloying agent to improve the strength, toughness, and wear resistance of steel. Approximately 85% of the vanadium produced globally is used in steel manufacturing. Vanadium steel alloys are used in tools, construction rebar, pipelines, automotive parts, and jet engines due to their high tensile strength and resistance to corrosion. Vanadium is used in the aerospace industry for manufacturing high-strength, lightweight titanium alloys. These alloys are critical in aircraft, spacecraft, and military equipment like jet engines, armour plating, and missile casings. Vanadium pentoxide (V₂O₅) is used as a catalyst in the production of sulfuric acid, which is a fundamental chemical in industrial processes. It is also used in the manufacture of ceramics, pigments, and glass coatings. Vanadium Redox Flow Batteries (VRFBs) are a key technology for large-scale energy storage solutions. These batteries are highly durable, scalable, and can provide stable, long-duration energy storage, making them ideal for integrating renewable energy sources like solar and wind into the grid.
Vanadium’s role in energy storage, particularly in VRFBs, is expected to expand significantly. VRFBs offer a longer lifespan, rapid response, and the ability to discharge at 100% without damaging the battery. This makes them a promising technology for grid-scale energy storage, electric vehicle charging stations, and renewable energy integration. Vanadium catalysts are being explored to improve the efficiency of hydrogen production through electrolysis. As the demand for green hydrogen grows, vanadium’s role in enhancing electrolyser performance could be significant. Research is ongoing into developing new vanadium-based alloys with superior properties, such as heat resistance and anti-corrosion, for use in extreme environments like space exploration, nuclear reactors, and advanced manufacturing. Vanadium-containing alloys are being investigated for use in additive manufacturing (3D printing) to produce high-strength components for aerospace, automotive, and medical implants.
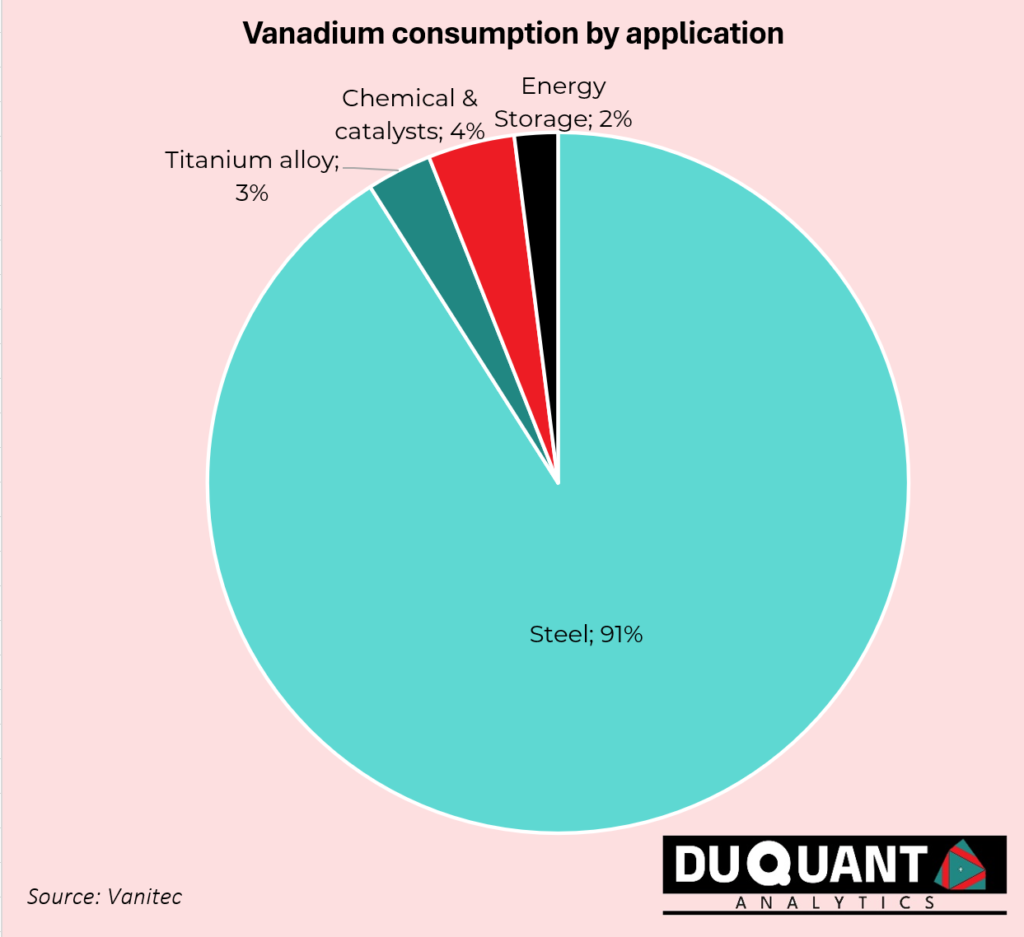
Vanadium compounds are being explored for their potential in environmental applications, such as the reduction of nitrogen oxides in industrial emissions. The automotive industry is increasingly using vanadium micro alloyed steels to reduce vehicle weight while maintaining strength, leading to improved fuel efficiency and lower emissions. Vanadium’s unique properties make it critical for a range of industries, from traditional steel production to cutting-edge energy storage solutions. Its role in green technologies, especially VRFBs, positions vanadium as a key element in the transition to a more sustainable energy future. Continued research into advanced alloys and catalytic applications will likely further expand its uses, highlighting vanadium’s growing importance in modern and future technologies.
Largest Sources and Producers of Vanadium
Vanadium is quite rare, and found in few regions worldwide, with major reserves located in countries such as China, Russia, South Africa, and Brazil. Geopolitically, these countries are at their core part of BRICS and not particularly western leaning. Historically Vanadium has had a tendency to have abrupt price surges due to supply shortfalls, and even in times of war due to its use in military equipment (armor-piercing projectiles, lightweight alloys used in aircraft & vehicles, missiles and rockets). Combining the supply side isolation risks, and use in high grade steel, Vanadium is a strategic metal to consider part of a portfolio.
According to the 2024 US Geological Survey (USGS), global vanadium reserves are estimated to be around 19 000 kilo tons. Australia holds the largest reserves (8500Kt or 45%), followed by Russia (5000Kt or 26%), China (4400kt or 23%) and South Africa (750kt or 4%), and Brazil (120Kt or 1%) which together dominate global vanadium supply. The remainder of the world accounts for a smaller share of reserves, with contributions from countries like Brazil, the United States, and Canada.
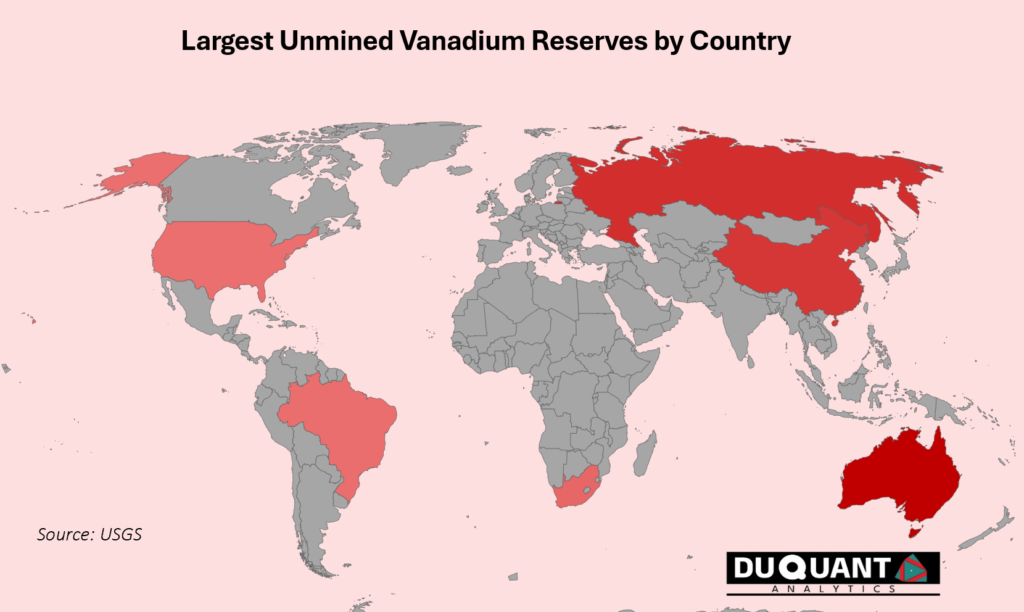
Since 2000, global vanadium mine production has increased significantly (148%, or 4.2% CAGR), driven primarily by China and Russia. China has been the dominant player, contributing around 53% of the total vanadium production over the last two and a half decades, followed by South Africa (23%), Russia (20%), and Brazil (3%).
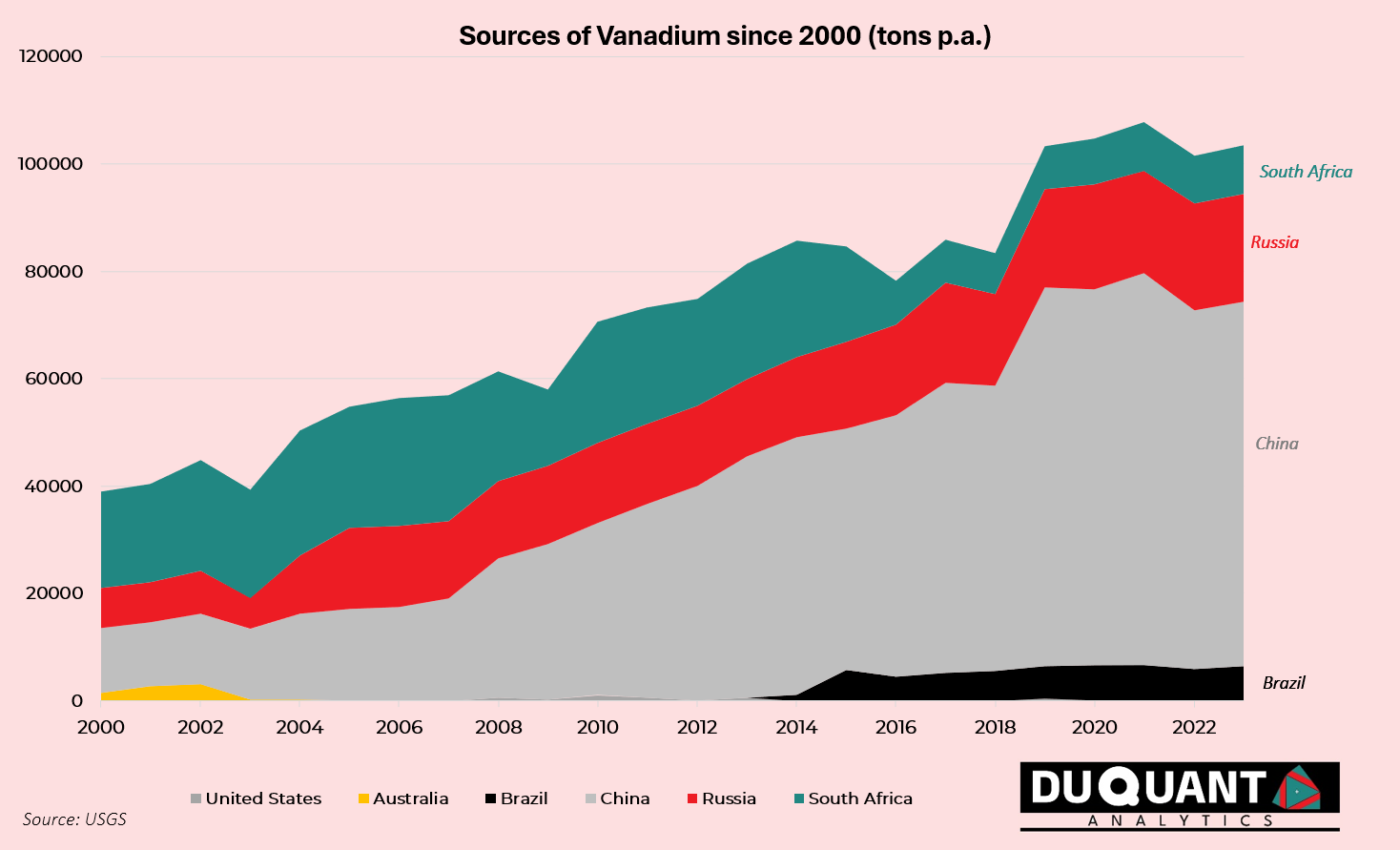
What is notable is that Australia has the largest reserves yet, accounted for less than 1% of the global total since year 2000. Australia’s large vanadium reserves have not translated into significant production due to economic, technical, lack of processing capacity & investment, as well as logistical factors. This combined with a greater focus on more profitable and in-demand commodities has meant Australia’s output is lagging its potential. However, with the increasing demand for vanadium, particularly for its use in energy storage and high-strength alloys, there may be future opportunities to develop Australia’s vanadium industry further.
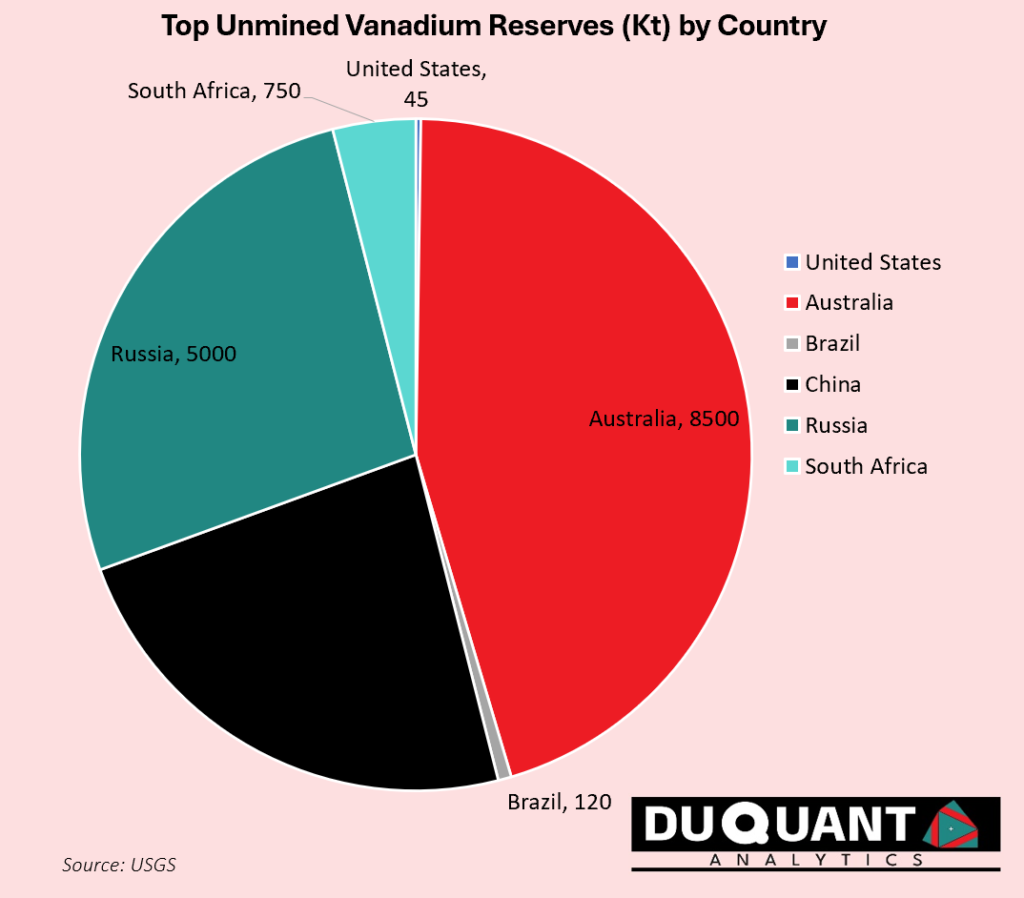
At current mining rates, the world has ~190 years of vanadium supply available from existing reserves, providing a stable long-term outlook for availability. However, excluding Australia this looks more like ~105 years. Price volatility remains a significant risk for vanadium mining companies.
The Remarkable History of Vanadium
Vanadium, a metal prized for its strength, corrosion resistance, and versatility in steel alloys, has a rich history filled with scientific discovery and industrial application. From its early discovery to its crucial role in modern technology, vanadium’s journey is a testament to human ingenuity and the ongoing quest for stronger, more durable materials. This narrative highlights key events and milestones that have shaped the vanadium industry over the centuries.
The story of vanadium begins in 1801 when the Spanish-Mexican scientist Andrés Manuel del Río discovered a new element in a sample of lead ore from Mexico. He initially named it “brown lead” (later renamed erythronium) due to the various colors its compounds exhibited. However, his discovery was met with skepticism, and the element was mistakenly thought to be impure chromium.
It wasn’t until 1830 that Swedish chemist Nils Gabriel Sefström rediscovered the element while working with iron ores. Sefström named it vanadium after Vanadis, the Norse goddess of beauty, due to the vibrant colors of its compounds. Shortly after, the metal was isolated by Friedrich Wöhler, solidifying its place on the periodic table.
The 19th century saw the gradual realization of vanadium’s potential, particularly in the production of steel. The first major application of vanadium was in the alloying of steel to produce stronger, more resilient materials. This was facilitated by the discovery of vanadium-rich minerals such as vanadinite and patronite.
Vanadium Steel: In 1905, the French metallurgist Henri Moissan and chemist Ferdinand Frédéric Henri Moissan first produced vanadium steel, demonstrating its superior strength and toughness. This discovery paved the way for the use of vanadium in the burgeoning automobile industry, where it was used to manufacture parts that required both light weight and high strength. The Ford Model T, for instance, utilized vanadium steel, significantly enhancing its durability and performance.
The early 20th century marked a period of significant expansion and technological advancements in the vanadium industry. As the demand for stronger and more durable materials grew, so did the production and application of vanadium.
By the 1920s, vanadium had become an essential component in the production of high-speed tools. Its ability to form stable carbides made it ideal for cutting tools that could withstand high temperatures and maintain their sharpness over prolonged use. This development was crucial for the manufacturing industry, leading to increased productivity and efficiency.
During World War II, vanadium’s strategic importance became evident. The metal was used extensively in the production of military vehicles, aircraft, and naval ships due to its ability to enhance the strength and durability of steel. Vanadium-alloyed armor plating and structural components provided crucial advantages in terms of protection and performance.
The post-war period saw a diversification of vanadium’s applications beyond steel alloys. Advances in chemistry and materials science opened up new possibilities for vanadium compounds in various industries.
In the 1950s and 1960s, vanadium compounds found new roles as catalysts in the chemical industry. Vanadium pentoxide, in particular, became widely used in the production of sulfuric acid, one of the most important industrial chemicals. Additionally, vanadium-based pigments were used to produce vibrant colors in ceramics, glass, and plastics.
The late 20th and early 21st centuries saw vanadium’s importance grow in the context of modern technology and sustainable energy solutions. During the 1980s, vanadium’s role expanded in the aerospace and defense industries. High-strength, lightweight vanadium alloys were used in the construction of advanced aircraft, spacecraft, and military hardware. These applications leveraged vanadium’s ability to improve the performance of titanium alloys, making them ideal for critical structural components.
The 21st century has seen a surge in interest in vanadium for energy storage applications. The development of vanadium redox flow batteries (VRFBs) represented a significant breakthrough in renewable energy storage. VRFBs offer the potential for large-scale energy storage with the ability to store and release energy efficiently. This technology is seen as crucial for stabilizing power grids that rely on intermittent renewable energy sources like wind and solar power.
The 2010s marked a growing global focus on sustainable energy solutions, leading to increased demand for vanadium. VRFB technology gained traction as a promising solution for energy storage, capable of supporting large-scale renewable energy projects. The ability of VRFBs to provide long-duration energy storage made them attractive for applications ranging from grid stabilization to remote power supply.
The 2020s have been characterized by continued innovation and a focus on environmental considerations in the vanadium industry. Efforts to improve the efficiency and cost-effectiveness of VRFBs have intensified, with ongoing research aimed at enhancing their performance and scalability. Additionally, the industry has increasingly emphasized sustainable mining practices and the recycling of vanadium-containing materials to reduce environmental impact.
Looking ahead, vanadium’s role in advanced technologies and sustainability is set to expand. Research and development efforts are focused on improving the performance of vanadium alloys, enhancing the efficiency of VRFBs, and exploring new applications in emerging fields such as 3D printing and advanced manufacturing.
Vanadium’s journey from a colorful curiosity to a critical component in modern technology underscores its unique properties and enduring value. Its story reflects the dynamic interplay between scientific discovery and technological advancement, shaping the future of industries ranging from aerospace to renewable energy. As the world continues to prioritize sustainability and innovation, vanadium’s importance is poised to grow, driving progress and transforming possibilities across a wide range of applications.
Navigating Vanadium
Navigating Vanadium Vanadium, a metal that strengthens steel to make it twice as resilient, and…