
Navigating Rare Earths
Scientific Properties of Rare Earth Elements
Rare earth elements (REEs) encompass a group of metals including lanthanum (La), cerium (Ce), neodymium and praseodymium (NdPr), dysprosium (Dy), and terbium (Tb). They are typically found in rare earth minerals such as bastnäsite, monazite, and xenotime. REEs exhibit unique magnetic, catalytic, and optical properties, vital for advanced technologies including electronics, renewable energy applications, and defence systems.
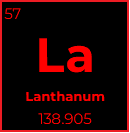
Lanthanum: with an atomic number of 57, is a silvery-white, soft metal that belongs to the lanthanide series of the periodic table. It has a melting point of 920 °C and a boiling point of 3464 °C, with a density of 6.145 g/cm³. Lanthanum is highly reactive, especially with water and air, where it forms lanthanum hydroxide (La(OH)₃) when exposed to water. It also readily reacts with halogens, acids, and bases. The element primarily exists in a +3 oxidation state and is used in various applications, including the production of catalysts, optical glasses, and in battery electrodes.
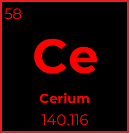
Cerium: with atomic number 58, is a ductile, silvery-white metal, known for being the most abundant of the rare earth elements. It has a melting point of 798 °C, a boiling point of 3443 °C, and a density of 6.770 g/cm³. Cerium is chemically reactive and readily reacts with water to form cerium hydroxide (Ce(OH)₃). It can exist in both +3 and +4 oxidation states, with the +4 state being particularly significant in industrial applications, such as in catalytic converters for automobiles. Cerium is also used in glass polishing, self-cleaning ovens, and as a component in lighter flints.
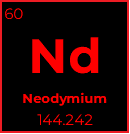
Neodymium: with an atomic number of 60, is a silvery-white, malleable metal. It has a melting point of 1024 °C, a boiling point of 3074 °C, and a density of 7.007 g/cm³. Neodymium reacts slowly with water, forming neodymium hydroxide (Nd(OH)₃), and predominantly exists in the +3 oxidation state. This element is best known for its strong magnetic properties, especially when alloyed with iron and boron to produce neodymium magnets (Nd₂Fe₁₄B), which are among the strongest permanent magnets available. These magnets are widely used in electronics, electric motors, and wind turbines.
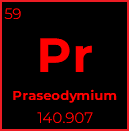
Praseodymium: with atomic number 59, is a soft, silvery metal with a melting point of 931 °C, a boiling point of 3520 °C, and a density of 6.773 g/cm³. This element reacts slowly with water to form praseodymium hydroxide (Pr(OH)₃) and typically exhibits a +3 oxidation state, though it can also show a +4 state in some compounds. Praseodymium is used in the production of strong permanent magnets and high-strength metal alloys. It is also employed in creating yellow pigments for ceramics and glasses, and in the production of specialized glasses for welders and glassmakers.
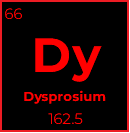
Dysprosium: with an atomic number of 66, is a silvery-white, soft metal that is known for its excellent magnetic properties and high neutron absorption capacity. It has a melting point of 1412 °C, a boiling point of 2567 °C, and a density of 8.540 g/cm³. Dysprosium reacts slowly with water, forming dysprosium hydroxide (Dy(OH)₃), and it generally exists in the +3 oxidation state. This element is essential in the production of high-temperature magnets and in nuclear reactors, where its high neutron absorption makes it valuable for control rods. Dysprosium is also used in various electronic devices and in the manufacture of laser materials.
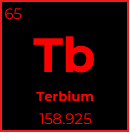
Terbium: with atomic number 65, is a silvery-gray, soft metal with a melting point of 1356 °C, a boiling point of 3230 °C, and a density of 8.230 g/cm³. It reacts slowly with water, forming terbium hydroxide (Tb(OH)₃), and typically exists in the +3 oxidation state, although +4 can also occur in certain compounds. Terbium is particularly valued for its use in solid-state devices, green phosphors in colour television tubes, and as a dopant in various materials. It also plays a role in the production of strong permanent magnets when combined with other rare earth elements like dysprosium.
Uses and Future Applications of Rare Earth Elements
When looking at the critical metals and elements that will benefit from a green energy transition, rare earth elements are a unique category due to its use in high end technologies and use cases.
Each individual rare earth element has its own unique applications and will be discussed further below. Overall, grouping the rare earths together, the largest demand and use for rare earths is in catalysts at 24% (CO2 emission reduction), high end magnets (23%), Polishing (12%), Metallurgy (8%), Batteries (8%), Glass (7%) and Ceramics (6%). This is according to a paper published 2018, (Goodenough K.M, Wall F., & Merriman D., 2018). The uses are diverse, and also in critical segments within the modern, and future economy.
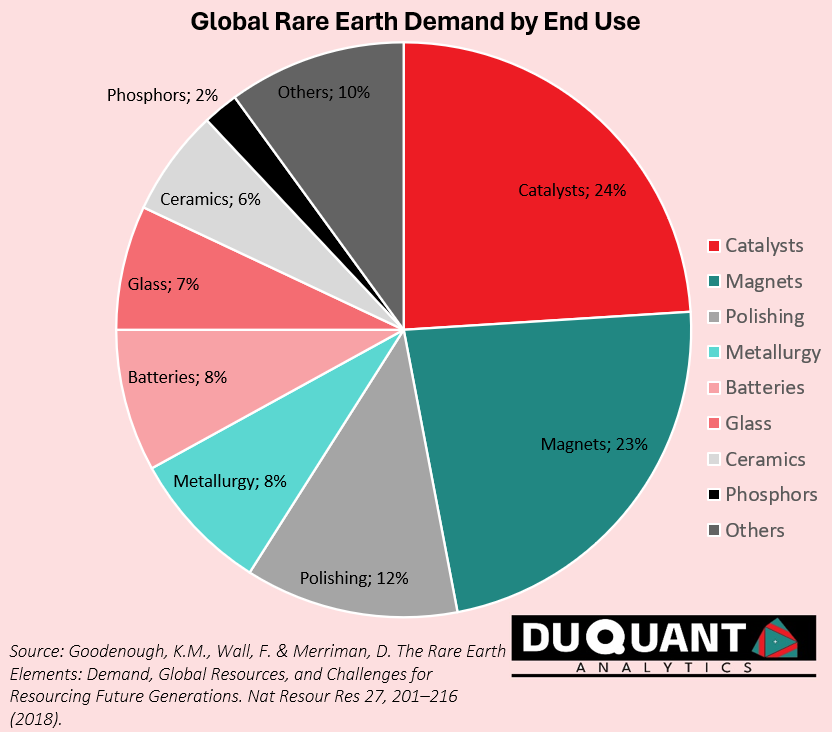
Lanthanum (la): is primarily used as a catalyst in petroleum cracking/refining processes (~40%-50% of demand), which convert heavy hydrocarbons into lighter, more valuable products like gasoline and diesel. Other major uses for lanthanum are in battery alloys (~20%-30% of demand) which is a key component in nickel-metal hydride (NiMH) batteries. This is particularly in hybrid vehicles like the Toyota Prius (containing ~10kg of lanthanum). Lanthanum oxide is also used in optical glass applications (~10%-15% of demand), such as camera and telescope lenses. Lanthanum improves the refractive index and durability of optical glasses used in cameras, binoculars, and other devices. Lanthanum is also used to form alloys that can absorb large amounts of hydrogen, making it useful in hydrogen storage technologies, although this makes up less than 10% of demand.
Future growth drivers for lanthanum will be a global shift towards electric vehicles (EVs), particularly hybrids, which are expected to drive demand for NiMH batteries. Growth in the global refining industry and continuous demand for refined petroleum products support lanthanum’s use in FCC catalysts. The growing need for high-performance optics in consumer electronics, robotics and military applications will also sustain lanthanum demand.
Cerium (Ce): The main use of cerium is in automotive catalysts (~40%-50% of demand) that reduce harmful emissions. Cerium plays a crucial role in facilitating the oxidation of carbon monoxide and hydrocarbons. The second largest use of cerium (~25%-30% of demand) is in the production of glass and ceramics, as well as particularly as a polishing agent that helps to improve the quality and clarity of glass products. Cerium oxide is also used in polishing powder for silicon wafers and other precision optical components. Cerium also has use in mischmetal, used in steel and aluminium alloys to improve their properties, comprising ~5%-10% of the demand.
Future growth drivers will be driven by environmental regulations, and stricter emissions standards globally will continue to drive demand for cerium in catalytic converters. Consumer electronics also remain a large market as the increased production of smartphones, tablets, and other devices with glass displays will sustain cerium demand in glass polishing.
Neodymium (Nd): a critical component in permanent magnets, such as neodymium-iron-boron (NdFeB) magnets, which are used in electric motors, wind turbines, hard disk drives, and various electronic devices. Neodymium use in magnets accounts for most of the demand (approximately 80-90%). Another use case is in lasers and glass where neodymium-doped lasers are used in medical and industrial applications, and neodymium is also used to colour glass.
Future growth drivers will be the rapid transition to renewable energy, particularly for magnets in electric motors in electric vehicles, and in wind power that contains NdFeB magnets in wind turbines. The electronics sector is also poised to continue to grow underpinned by consumer electronics, hard drives and data storage solutions which should see sustained demand for neodymium.
Praseodymium (Pr): is used in combination with neodymium to create high-strength magnets (NdPr magnets), accounting for about 30-35% of praseodymium demand. Praseodymium is also used in high-strength alloys for aircraft engines, contributing to about 20% of its demand. Praseodymium is used as colouring agents to create yellow pigments in ceramics and glasses.
Future growth drivers would be high end magnets for EVs and Wind Turbines. The same trends driving neodymium demand—renewable energy and electric vehicles—will also drive praseodymium demand in the magnet industry. Growth in the aerospace sector, particularly in the production of lighter, stronger materials, will also boost demand for praseodymium-containing alloys. Consumer & luxury products would also be a driver for the use of praseodymium in pigments for high-quality ceramics and glassware. This segment may see modest growth with rising consumer demand for decorative items.
Dysprosium (Dy): is used to enhance the heat resistance of NdFeB magnets (high temperature magnets), which are crucial for high-performance motors in EVs and wind turbines. This application accounts for about 90% of dysprosium demand. Nuclear Reactors: Dysprosium’s neutron absorption properties make it useful in control rods for nuclear reactors, representing about 5% of its demand.
Future growth drivers for dysprosium is the increased adoption of electric vehicle, which will drive the demand for dysprosium-enhanced magnets that can withstand higher temperatures without losing their magnetic properties. The expansion of wind power capacity globally will also support dysprosium demand in wind turbines. Further, increased adoption of nuclear energy, with proven and safe use cases, presents the potential resurgence of nuclear energy as a low-carbon power source could boost demand for dysprosium in reactor components.
Terbium (Tb): a key component in green phosphors used in fluorescent lamps and colour displays, accounting for about 50-60% of terbium demand. Like dysprosium, terbium is also used in NdFeB magnets to improve temperature resistance, representing about 20-25% of its demand. Terbium is also used in various solid-state devices and in certain laser materials.
Future growth drivers include display technology, with the ongoing demand for high-quality displays in televisions, smartphones, and tablets will sustain terbium demand in phosphors. The push for more energy-efficient lighting and display technologies could also increase the need for terbium-based phosphors. The growing use of advanced magnets, i.e. NdFeB magnets in EVs and wind turbines, will likely drive demand for terbium, particularly as manufacturers seek to improve the performance of these magnets under high-temperature conditions.
Largest Sources and Producers of Rare Earth Elements
One of the major risks facing rare earth supply globally, is the high concentration to China (~79% of all primary supply globally). Thus, China will be a key player in sourcing the rare earths required for producing high end magnets in the renewable energy transition, as they are required for EV motors and wind turbines.
Rare Earth elements are found in few places around the world and according to the 2024 US Geological Survey (USGS), global rare earth reserves stand at 110,000 Kilo tons (Kt) with the largest reserves being China (44,000 Kt), Vietnam (22,000 Kt), Brazil (21,000 Kt), Russia (10,000 Kt), India (6,900 Kt) and Australia (5,700 Kt). The remainder of the world makes up only 5,815 Kt (or 5%).
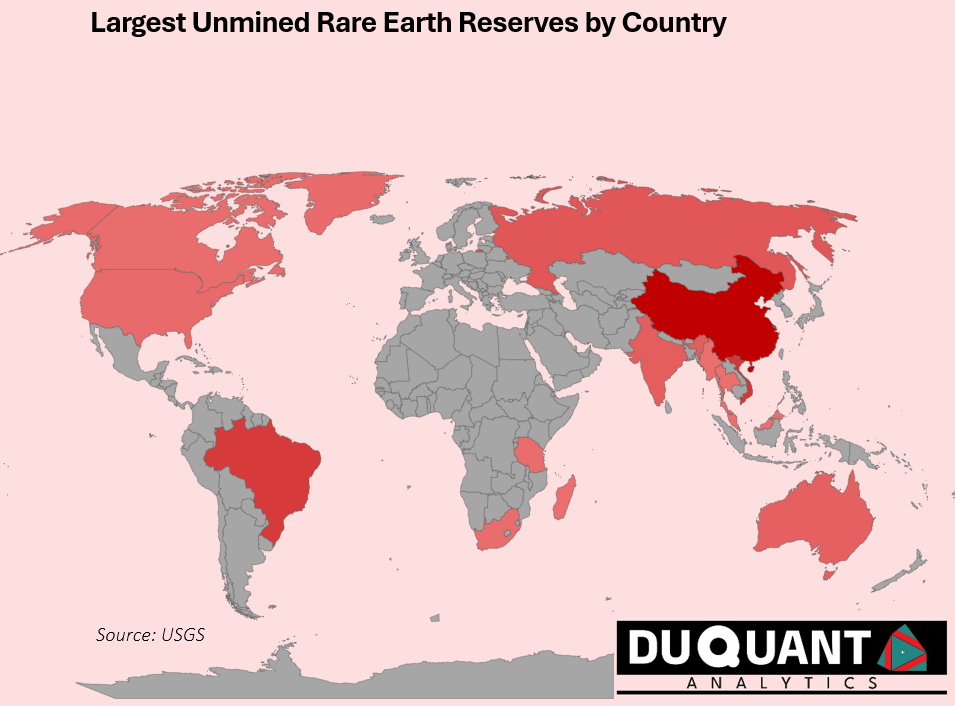
Rare Earth mine production since year 2000 has increase over 278% to 2023, from 92.7 kt to 350kt. Majority of this increase can be attributed to China. In terms of total annual mine production, since 2000 approximately 79% of Rare Earths came from China, followed by USA (6%), Australia (5%), and Burma (5%). The rest of the world only makes up 5%.
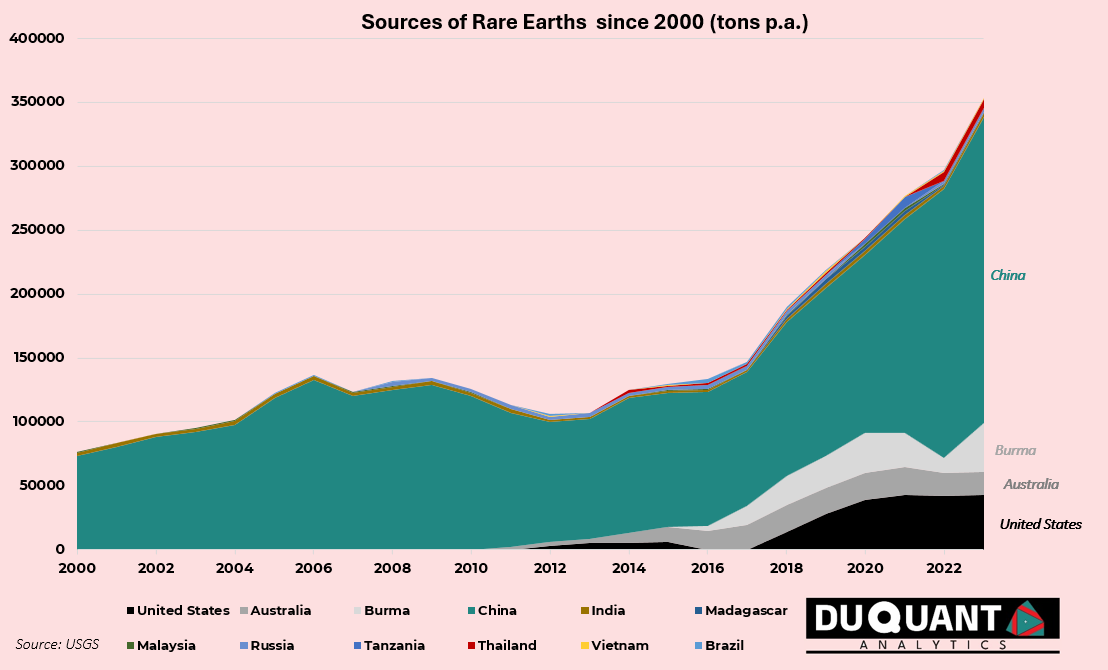
At current mine production rates and reserves, the world has plenty of rare earths, with c.314 years left of mining on existing reserves. The main risks are the concentration of reserves to few regions, with 40% being China, followed by Vietnam (20%), Brazil (19%), Russia (9%), India (6%), and Australia (5%). Note that in 2023, c.11% of supply came from Burma (a.k.a. Myanmar), while Burma reserves are not disclosed by the USGS, and there have been reports that rare earth mining in the region is unregulated at present.
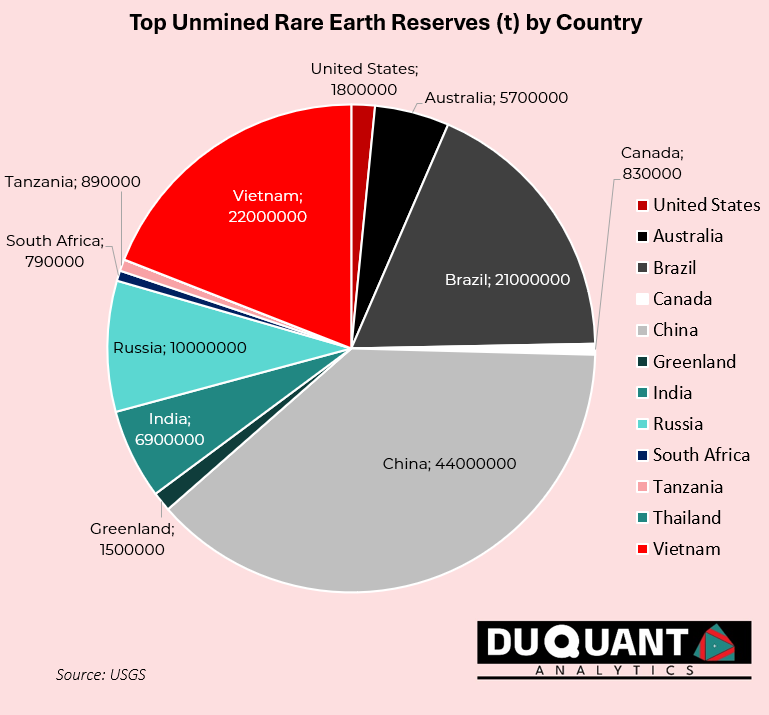
The Remarkable History of Rare Earths
Rare earth elements (REEs) are a group of 17 metals, including the lanthanides plus scandium and yttrium, that are essential for a multitude of modern technologies. Their journey from obscurity to critical materials for advanced applications is a captivating story of scientific discovery, technological innovation, and geopolitical intrigue. Key rare earth elements such as lanthanum, cerium, neodymium, praseodymium, dysprosium, and terbium play pivotal roles in this narrative.
The Early Discoveries: 18th and 19th Centuries
The story of rare earth elements begins in the late 18th century with the discovery of the first rare earth mineral. In 1787, Swedish army lieutenant Carl Axel Arrhenius found an unusual black rock near the village of Ytterby in Sweden. This mineral, later named gadolinite, contained several previously unknown elements, leading to the identification of what we now call rare earth elements. Later in 1794, Finnish chemist Johan Gadolin isolated an oxide, later named yttria, from this mineral, marking the discovery of the first rare earth element, yttrium. Over the next century, chemists identified more rare earth elements from various minerals. Cerium was discovered in 1803 by Swedish chemists Jöns Jacob Berzelius and Wilhelm Hisinger, as well as independently by German chemist Martin Heinrich Klaproth. Lanthanum was isolated in 1839 by Swedish chemist Carl Gustaf Mosander, who later also discovered terbium (1843) and erbium (1843).
The Industrial Age: 20th Century
The early 20th century saw the first significant industrial uses of rare earth elements. Cerium became widely used in gas mantles for lighting, while mischmetal, an alloy of cerium and lanthanum, was employed in lighter flints. These applications, although limited, highlighted the unique properties of rare earth elements and their potential for various technological applications. The mid-20th century marked a turning point in the utilization of rare earth elements in high end technology. During World War II, the demand for better radar and communication systems led to increased research into rare earth elements. Europium, for instance, became crucial for producing red phosphors in color television tubes.
Lanthanum and cerium, the most abundant rare earth elements, found widespread use in various applications. Lanthanum was used in camera lenses and optical glass due to its ability to improve clarity and reduce chromatic aberration. Cerium, on the other hand, was vital in the automotive industry for catalytic converters, which reduce harmful emissions from vehicles.
Neodymium and praseodymium gained prominence in the late 20th century with the development of high-strength permanent magnets. Neodymium-iron-boron (NdFeB) magnets, developed in the 1980s, revolutionized the electronics industry by enabling the miniaturization of devices while improving performance. These magnets are now used in everything from headphones and computer hard drives to wind turbines and electric vehicle motors.
Dysprosium and terbium are essential for enhancing the performance of neodymium magnets, particularly in high-temperature applications. Dysprosium is added to NdFeB magnets to improve their resistance to demagnetization, making them suitable for use in electric vehicles and wind turbines. Terbium is used in green phosphors for fluorescent lamps and in solid-state devices.
The late 20th century saw China emerge as the dominant player in the rare earth industry. With vast deposits and low-cost production methods, China quickly became the world’s leading producer of rare earth elements. By the 1990s, China controlled over 90% of global rare earth production, a position it still holds today.
Noteworthy Events in the 21st Century
The early 2000s witnessed a technology boom that significantly increased the demand for rare earth elements. The proliferation of smartphones, laptops, and other electronic devices drove up the need for high-performance materials, particularly rare earth magnets and phosphors.
In 2010, China’s decision to restrict rare earth exports sent shockwaves through global markets. Prices for rare earth elements soared, highlighting the world’s dependence on China for these critical materials. This event prompted countries and companies to seek alternative sources and invest in recycling and substitution technologies.
By 2015, the focus on sustainable and ethical sourcing of rare earth elements intensified. Efforts to reduce environmental impact and improve mining practices gained momentum. Recycling of rare earth elements from electronic waste also became a significant area of research and development.
The 2020s have been characterized by a rapid transition to renewable energy and electric transportation. Rare earth elements are crucial for wind turbines and electric vehicle motors, leading to a surge in demand. Governments worldwide have implemented policies to promote green technologies, further boosting the need for rare earth elements.
Environmental Considerations and Sustainability
The extraction and processing of rare earth elements pose significant environmental challenges. The mining process often generates large amounts of toxic waste, which can contaminate soil and water. To address these issues, the industry has increasingly focused on developing more sustainable and environmentally friendly mining practices. Recycling rare earth elements from end-of-life products is also becoming an important strategy to reduce reliance on primary sources and minimize environmental impact.
The Future: A Metal for Advanced Technologies
As the world continues to advance technologically, the importance of rare earth elements is set to grow. These elements are indispensable for the development of next-generation technologies, including more efficient electric vehicles, advanced wind turbines, and cutting-edge electronics.
Ongoing research aims to improve the extraction and processing of rare earth elements, enhance recycling methods, and develop alternative materials that can reduce dependence on critical rare earths. The future of rare earth elements is closely tied to the global push for sustainability, innovation, and energy efficiency. From their early use in pigments and glass to their central role in modern technology, the journey of rare earth elements is a testament to their enduring value and versatility. Their story reflects the dynamic interplay between natural resources and technological advancements, shaping the future of our high-tech world.
More posts on Rare Earth Elements:
Navigating Rare Earth Elements
Navigating Rare Earth Elements Can the supply of rare earth elements keep up with the…