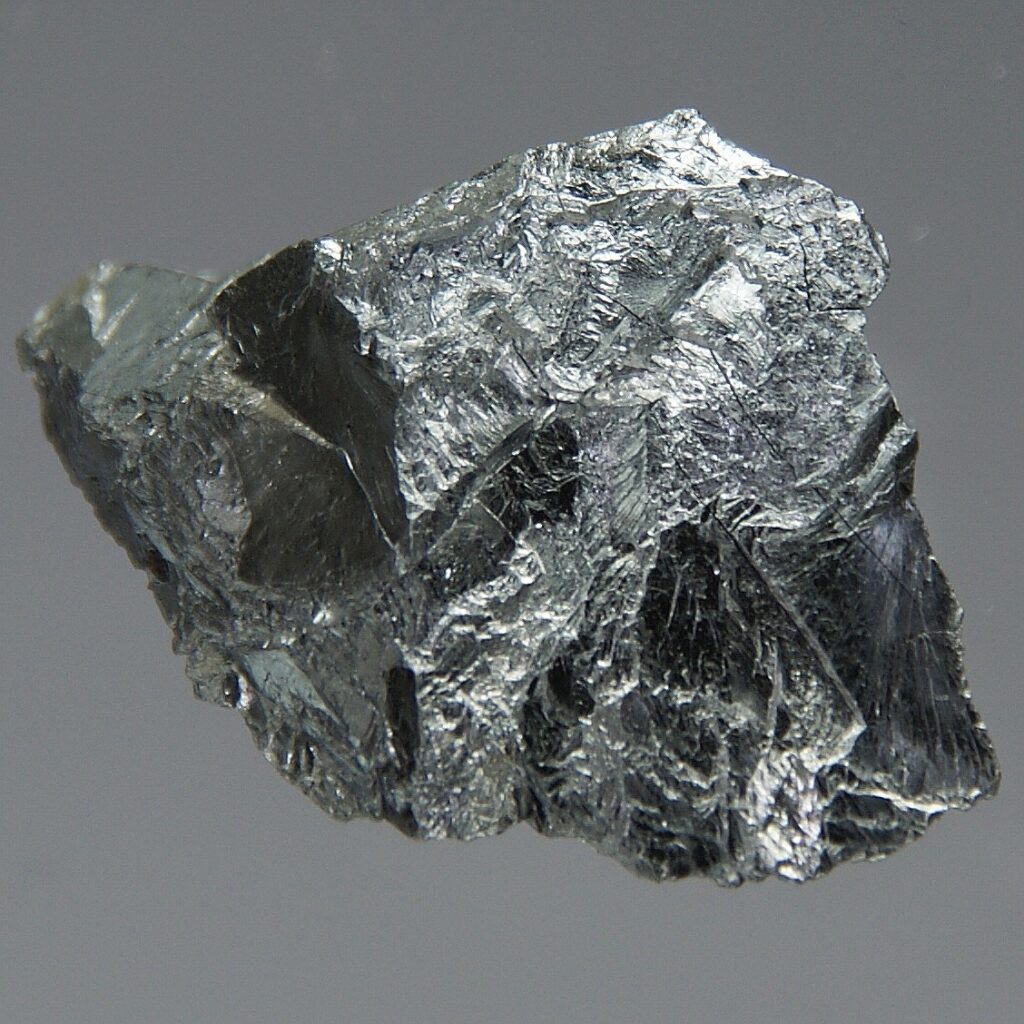
Navigating Chromium (Cr)
Scientific Properties of Chromium
Chromium is a hard, lustrous transition metal with atomic number 24 and symbol Cr. It has a high melting point of 1,857°C and is primarily found in chromite ore. Chromium is extracted through metallurgical processes and forms a stable oxide layer that provides excellent corrosion resistance. It is used extensively in stainless steel production, chrome plating, and as an alloying element in aerospace alloys and refractory materials.

Uses and Future Applications
Chromium is a critical industrial metal with diverse applications, primarily known for its role in the production of stainless steel and various alloys.
Stainless Steel Production (85%): The largest use of chromium is in the production of stainless steel, where it enhances corrosion resistance, hardness, and strength. Stainless steel is used extensively in construction, automotive, household appliances, and various industrial applications. Stainless steel typically contains 10-30% chromium by weight, depending on the grade. This is between 100kg to 300Kg of chromium per 1000kg of stainless steel.
Alloying Agent (10%): Chromium is used as an alloying agent in the production of non-ferrous alloys, superalloys, and other specialty steels. These alloys are crucial for aerospace, power generation, and military applications due to their ability to withstand extreme temperatures and mechanical stress.
Refractory and Foundry Sands (2%): Chromium is used in the production of refractory materials and foundry sands, which are essential in high-temperature industrial processes, such as the production of metals, glass, and ceramics.
Chemicals and Pigments (2%): Chromium compounds, such as chromates and dichromates, are used in the chemical industry for various applications, including pigments, tanning leather, and corrosion inhibitors.
Other Uses (1%): Chromium finds minor applications in areas such as plating, catalysts, and synthetic rubies for lasers.
These estimates highlight the dominant role of stainless steel production in driving chromium demand, followed by its significant use in various high-performance alloys and industrial applications. The continued growth in infrastructure development, automotive manufacturing, and industrial activities is expected to sustain and potentially increase the demand for chromium in the future.
Largest Sources and Producers of Chromium
Chromium is typically found in large, layered igneous intrusions like the Bushveld Complex in South Africa and the Great Dyke in Zimbabwe. These deposits form through magmatic differentiation, where chromium-rich minerals settle out from a magma chamber and accumulate in layers. These are known also as Stratiform Chromite Deposits. Chromium is also found in Podiform Chromite Deposits, such as in India, Turkey and Kazakhstan and are typically associated with ophiolite complexes, found in tectonic settings like oceanic crust. These deposits form through processes related to mantle melting and deformation, often smaller and irregular compared to stratiform deposits.
According to the 2024 US Geological Survey (USGS), global Chromium reserves stand at 560,000 Kilo tons (Kt or 1000t) with the largest reserves being Kazakhstan (230,000Kt), South Africa (200,000 Kt), India (79,000 Kt), Turkey (27,000 Kt), and Finland (8,300 Kt). The remainder of the world makes up only around 3% of global chromium reserves.
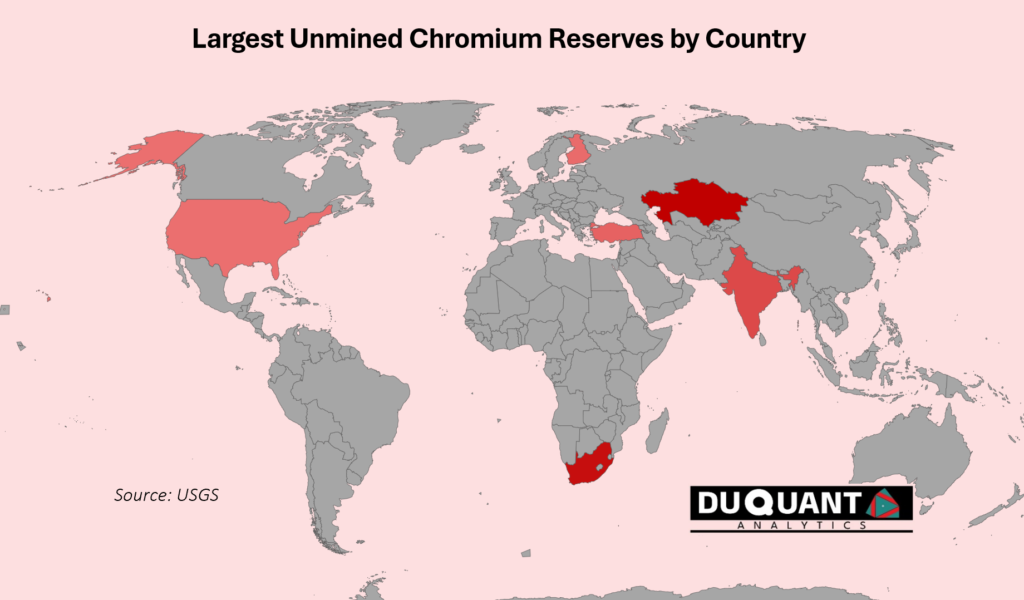
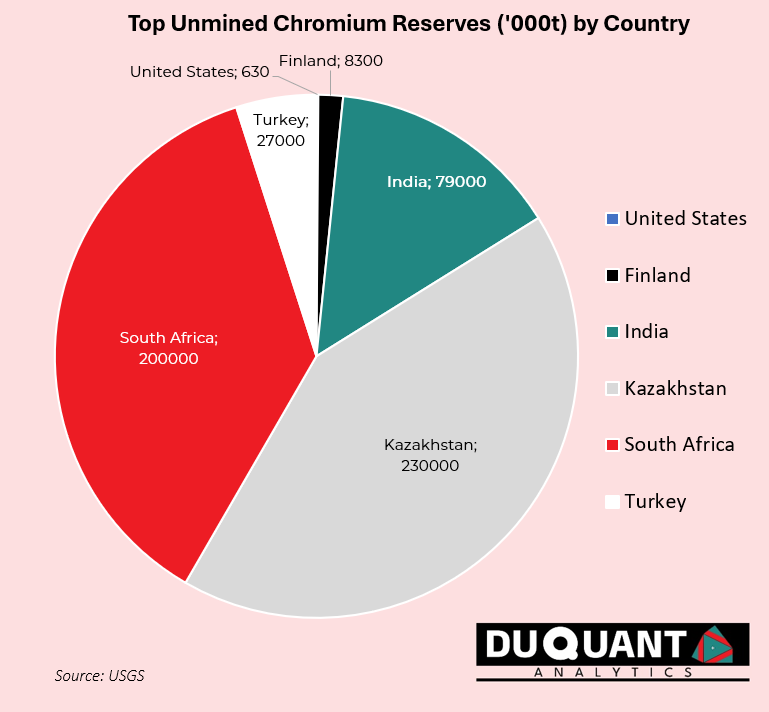
Chromium mine production from 2017 to 2023 has decreased at a CAGR of -0.9% to an annual supply of 41,000 Kt in 2023. The majority of this decrease can be attributed to COVID-19 lockdowns, which heavily impacted stainless steel demand, and impacted the large exporters of chromium like South Africa and Turkey. In terms of total annual mine production, since 2000 approximately 43% of Chromium came from South Africa, followed by Kazakhstan (16%), Turkey (13%), India (11%), and Finland (4%). The rest of the world has made up c.13% of the total mined supply of chromium since year 2000.
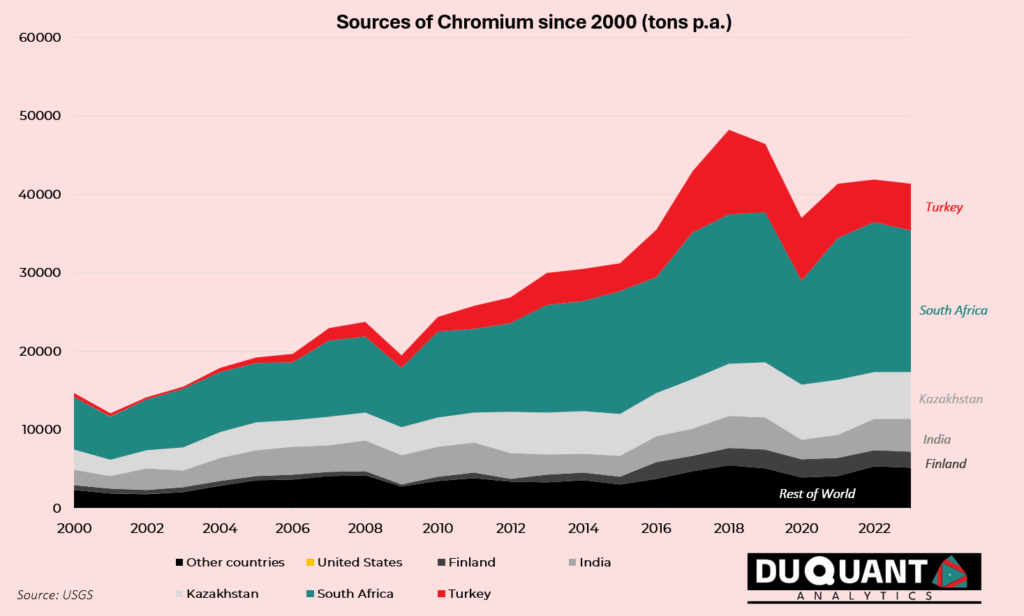
Based on the current annual production rate, and the estimated global reserves, there is c.13 years remaining of Chromium supply and thus could be a big exploration and investment drive to increase global reserves in the next decade.
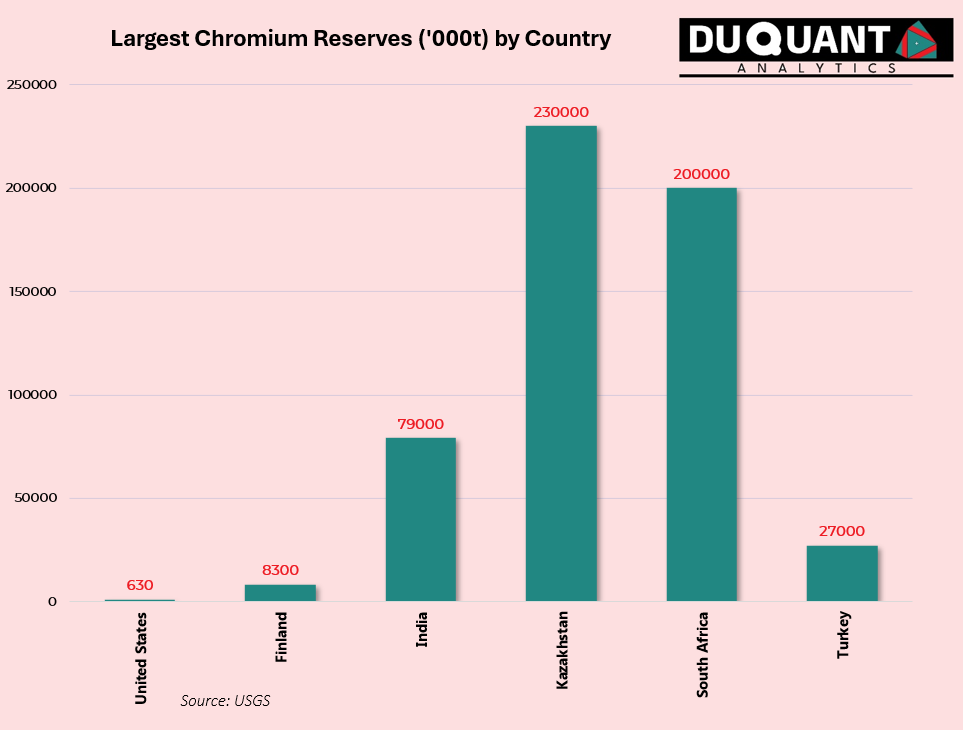
The Remarkable History of Chromium
Chromium, a metal known for its brilliant shine and corrosion resistance, has a rich and varied history that spans from ancient times to its critical role in modern technology. Its journey from an intriguing mineral to an indispensable industrial element showcases its unique properties and the ingenuity of those who harnessed its potential. This narrative highlights key events and milestones that have shaped the chromium industry over the centuries.
Chromium’s story begins long before it was isolated as an element. The ancient Chinese were among the first to use chromium compounds, dating back to at least 200 BCE. Chinese artisans used chromite, the primary ore of chromium, to craft weapons and tools with enhanced durability and resistance to corrosion.
During the Qin Dynasty (221-206 BCE), Chinese blacksmiths utilized chromium in the production of their weapons. The famous Terracotta Army, buried with China’s first emperor Qin Shi Huang, was armed with swords and other weapons plated with a chromium compound to prevent rusting, demonstrating an early understanding of chromium’s protective properties.
In 1761, the mineral crocoite (lead chromate) was discovered in the Ural Mountains of Russia by Johann Gottlob Lehmann. This strikingly vibrant mineral intrigued scientists due to its bright orange-red color. Crocoite became the key to discovering chromium.
The French chemist Louis Nicolas Vauquelin is credited with the isolation of chromium. In 1797, Vauquelin succeeded in isolating the metal by heating crocoite with charcoal. He named the new element “chromium” after the Greek word “chroma,” meaning color, due to the various colored compounds it could form. This discovery opened the door to chromium’s many applications.
Early 1800s: Chromium compounds quickly found uses in pigments and tanning. Chromium oxide green became a popular pigment in paints and dyes, valued for its stability and vibrant hue. Chromium salts were also used in the tanning of leather, significantly improving its durability and appearance.
The demand for chromium spurred the mining of chromite. The first significant chromite deposits were discovered in the United States in the early 1820s, particularly in Pennsylvania. These mines provided a steady supply of chromite for industrial uses, paving the way for further advancements.
The 20th century marked a period of rapid expansion and innovation for chromium, as its applications diversified and its industrial importance grew. One of the most significant developments in the history of chromium was its role in the invention of stainless steel. In 1913, British metallurgist Harry Brearley discovered that adding chromium to steel made it highly resistant to corrosion. This innovation led to the widespread adoption of stainless steel in various industries, from cutlery to construction, revolutionizing the materials used in everyday life. South Africa played an instrumental role in the stainless steel revolution following Harry Brearley’s 1913 discovery that adding chromium to steel significantly enhanced its resistance to corrosion and staining. With vast reserves of chromite ore in the Bushveld Igneous Complex (BIC), South Africa quickly emerged as a critical supplier of chromium, the key alloying element in stainless steel. Chromium’s ability to form a durable oxide layer on steel surfaces made it essential for applications ranging from construction to automotive and kitchenware. Following World War II, as countries industrialized and stainless steel demand surged, South Africa developed significant smelting and refining capabilities, supported by abundant chromite and cheap electricity from Eskom, solidifying its position as the world’s leading ferrochrome producer.
During World War II, chromium became a strategic material due to its crucial role in producing military equipment. Chromium-plated weapons, aircraft parts, and naval vessels benefited from its corrosion resistance and strength. The war effort increased the demand for chromium, leading to the exploration and development of new chromite deposits worldwide.
The post-war era saw further diversification of chromium’s applications, driven by technological advancements and industrial growth. In the 1950s and 1960s, the aerospace and automotive industries began to utilize chromium for its excellent properties. Chromium plating became standard for enhancing the durability and aesthetic appeal of vehicle parts, while high-temperature chromium alloys were used in jet engines and other aerospace applications. As the use of chromium expanded, so did awareness of its environmental and health impacts. Hexavalent chromium, a toxic form of the metal, posed significant health risks, leading to increased regulation and the development of safer alternatives. This period saw a growing emphasis on environmental protection and worker safety in chromium-related industries.
During the Cold War, the strategic importance of stainless steel for military and industrial applications further boosted global reliance on South Africa’s chromium resources. Despite international sanctions during apartheid, the country maintained its relevance through clandestine trade and domestic beneficiation efforts. Innovations in chromite processing and smelting allowed South Africa to navigate market volatility and meet growing global demand. By the mid-20th century, stainless steel had become a cornerstone of modern industry, and South Africa’s chromium resources were indispensable in its rise, leaving a legacy of metallurgical innovation and economic significance that endures to this day.
Chromium found new applications in the electronics and technology sectors. It became a vital component in the production of magnetic tapes and hard disks, crucial for data storage in computers and other devices. The development of thin-film technology also relied on chromium’s unique properties. In the 2000s, the chromium industry began to adopt more sustainable mining practices. Efforts to reduce the environmental impact of chromite mining included improved waste management, water conservation, and the rehabilitation of mined land. These practices aimed to balance industrial demand with environmental stewardship.
The 2010s saw an increasing focus on renewable energy technologies, with chromium playing a role in advancements such as high-performance batteries and fuel cells. Chromium-based materials were explored for their potential to enhance the efficiency and durability of these energy storage systems, contributing to the global transition to cleaner energy sources.
The 2020s have witnessed the rise of additive manufacturing (3D printing), where chromium-containing alloys are used to produce high-strength, corrosion-resistant components. This technology has applications in aerospace, medical devices, and industrial manufacturing, highlighting chromium’s ongoing importance in cutting-edge industries.
Looking ahead, chromium’s role in advanced technologies and sustainability is set to expand. Research and development efforts are focused on improving the performance of chromium-based materials, enhancing recycling methods, and exploring new applications in emerging fields such as nanotechnology and advanced manufacturing.
From its ancient use in weaponry to its critical role in modern technology, chromium’s journey is a testament to its versatility and enduring value. Its story reflects the dynamic interplay between scientific discovery and technological advancement, shaping the future of industries ranging from aerospace to renewable energy. As the world continues to prioritize sustainability and innovation, chromium’s importance is poised to grow, driving progress and transforming possibilities across a wide range of applications.
Navigating Chromium
Navigating Chromium High grade stainless steel would have less strength, durability and corrosion resistance if…