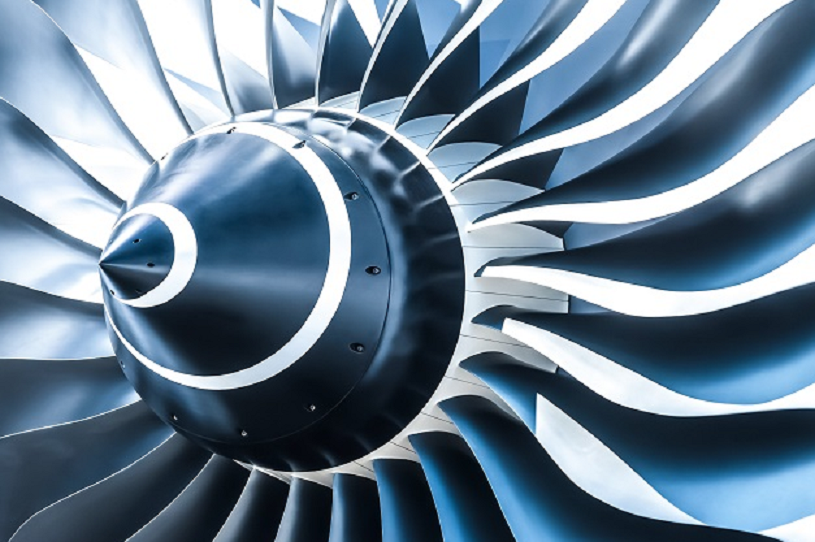
Navigating Titanium (Ti)
Scientific Properties of Titanium
Titanium (Ti), atomic number 22, is a lustrous transition metal known for its exceptional strength-to-weight ratio, corrosion resistance, and low density. With an atomic mass of 47.87 u, titanium has a high melting point of 1,668°C (3,034°F) and a boiling point of 3,287°C (5,949°F), making it stable under extreme temperatures. It has two primary crystalline structures: a hexagonal close-packed (hcp) alpha phase at lower temperatures and a body-centered cubic (bcc) beta phase at higher temperatures. Titanium’s strength, comparable to that of certain steels, is paired with a low density (about 60% of the density of steel), giving it superior strength without added weight. It’s resistant to oxidation and many chemicals, such as seawater and chlorine, due to a naturally forming oxide layer on its surface, which also enhances its biocompatibility.
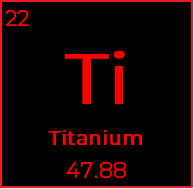
Uses and Future Applications
Titanium has a high strength-to-weight ratio, corrosion resistance, and biocompatibility, making it versatile across aerospace, military defence, medical and dental and a range of other applications. Titanium’s combination of properties makes it indispensable in numerous industries with one of the largest consumers being the aerospace industry, which relies on titanium for lightweight, high-strength components capable of withstanding extreme temperatures. ~15% of a Boeng 787’s body is titanium. The medical field also makes extensive use of titanium, especially in implants and surgical instruments, where its biocompatibility and resistance to corrosion are critical. In the chemical sector, titanium alloys are used in equipment exposed to corrosive environments, such as piping and reactors. Consumer electronics further leverage titanium’s light weight and durability for device casings and frames.
Titanium dioxide (TiO₂), derived from titanium, also plays a dominant role in the pigments industry. This compound is a widely used white pigment, valued for its brightness, opacity, and high refractive index, making it ideal for paints, coatings, plastics, and paper. It also provides UV-blocking capabilities, making it a common ingredient in sunscreens and cosmetics. Titanium dioxide is crucial in the construction and automotive industries, where high-quality finishes and durable coatings are needed, and as urbanization and infrastructure projects increase, so does demand for titanium-based pigments.
The demand for titanium across industries is on the rise, fueled by expanding applications in aerospace, construction, consumer products, and healthcare. Titanium’s role in greener technologies, including electric vehicle (EV) production and desalination plants, is also gaining importance. With new extraction and refinement methods, titanium’s future looks promising, with innovations aimed at more sustainable production, particularly in pigments, and broader adoption across emerging sectors.
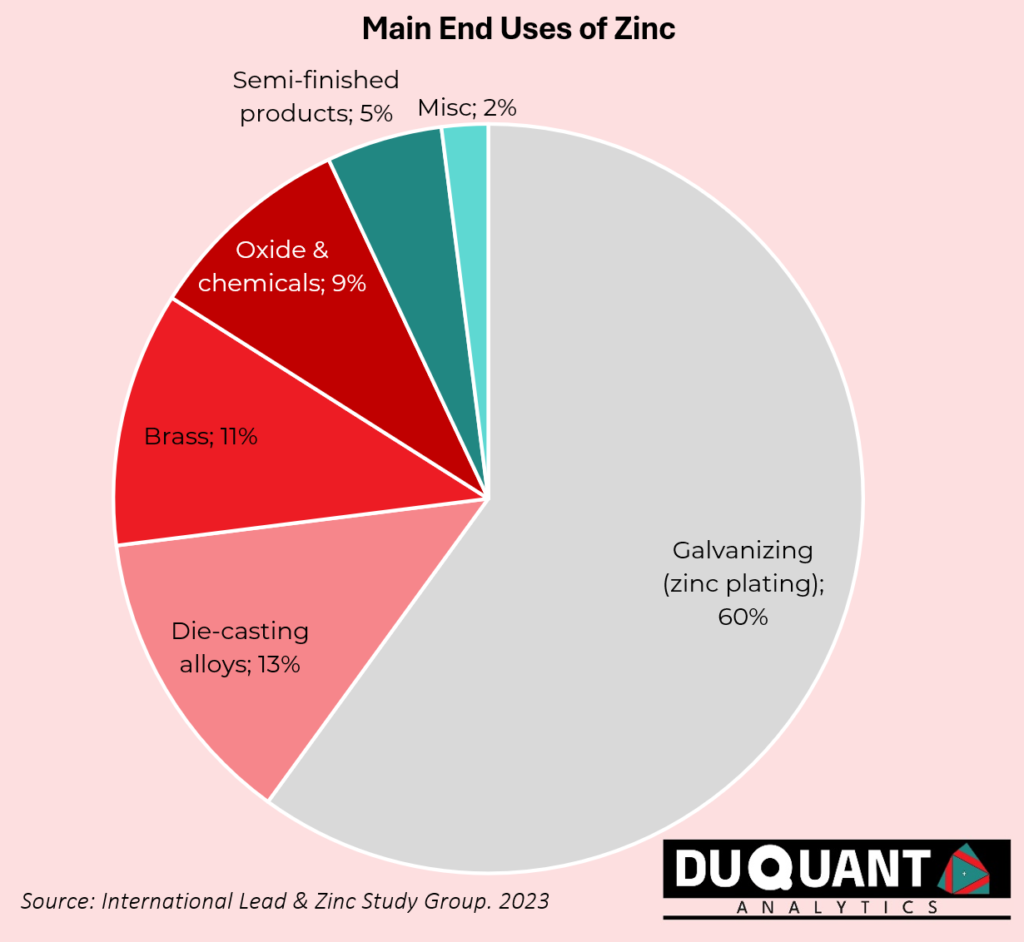
Largest Sources and Producers of Titanium
The titanium production process is quite a complex ecosystem and there are many steps and players involved along the way. The journey starts with mining titanium-containing minerals, such as ilmenite (FeTiO₃) or rutile (TiO₂), which are then processed into a concentrate.. Titanium ores and concentrates are mined from heavy mineral sands or hard-rock sources from many countries around the world. The ores are concentrated by separating the titanium-rich minerals (like ilmenite or rutile) from other minerals. Titanium content in rutile and ilmenite differs significantly and rutile is preferred due to its higher titanium grade and ease of processing, although ilmenite is more abundant and often used as a cost-effective alternative when processed to increase its TiO₂ content. Rutile (TiO₂) typically contains about 90–96% titanium dioxide (TiO₂), making it a high-grade titanium mineral. Ilmenite (FeTiO₃) generally has a lower titanium dioxide content, around 40–65% titanium dioxide, with the remaining portion primarily iron oxides.
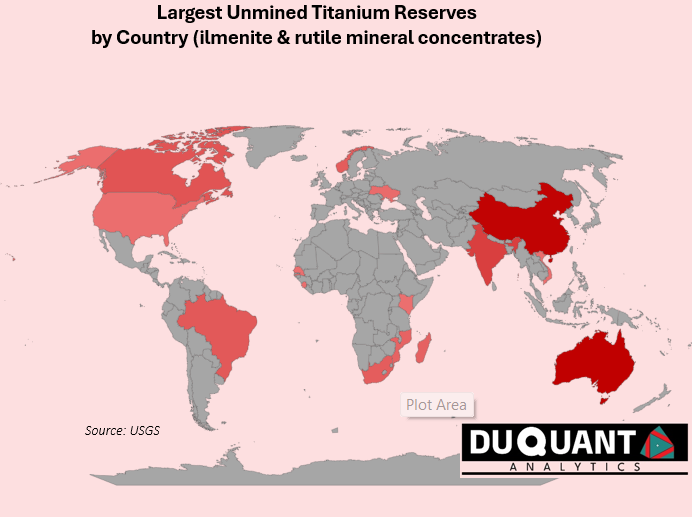
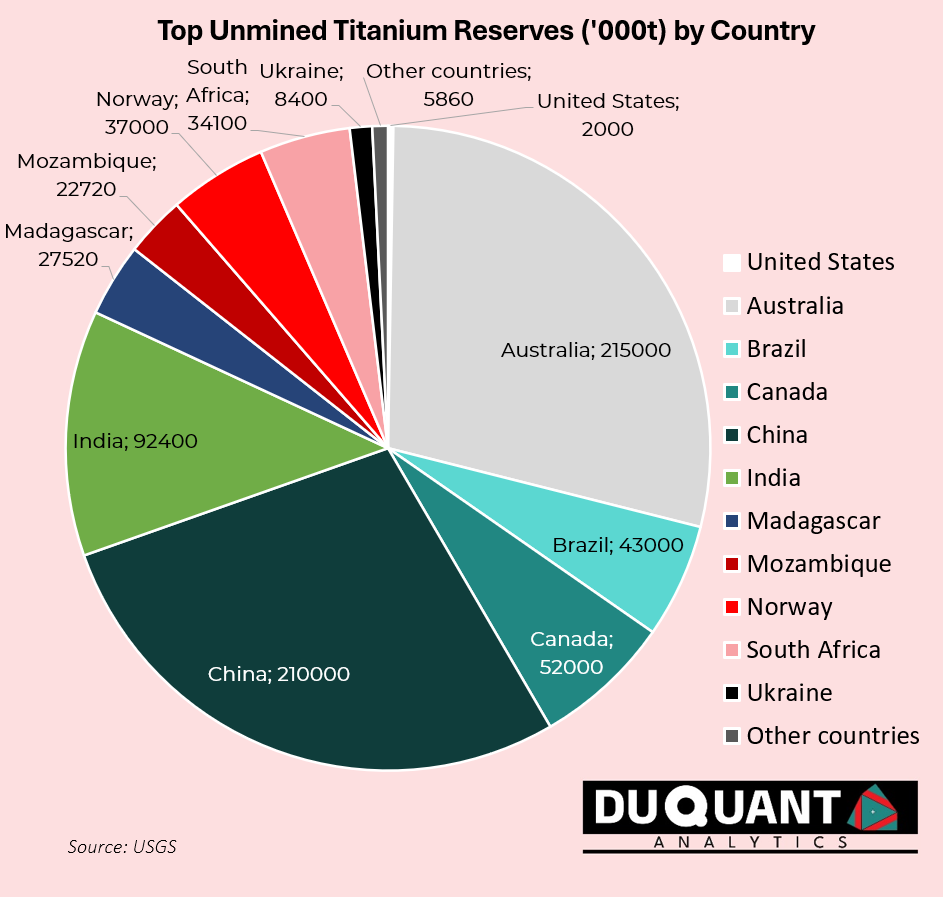
Australia and China have the largest reserves of Titanium concentrates (Rutile and Ilmenite), which are raw, naturally occurring titanium minerals mined directly from deposits. The smelting of ilmenite in a furnace separates out iron and increases the TiO₂ content, typically yielding a high-titanium slag with around 80-95% TiO₂. This refined product can be used as a substitute for natural rutile in certain applications, especially where high purity is needed. Over the last two decades, China (22%),South Africa (15%), Australia (13%) and Mozambique (10%) have been the largest sources of raw titanium concentrates, with the rest of the world making up the remaining 40%.
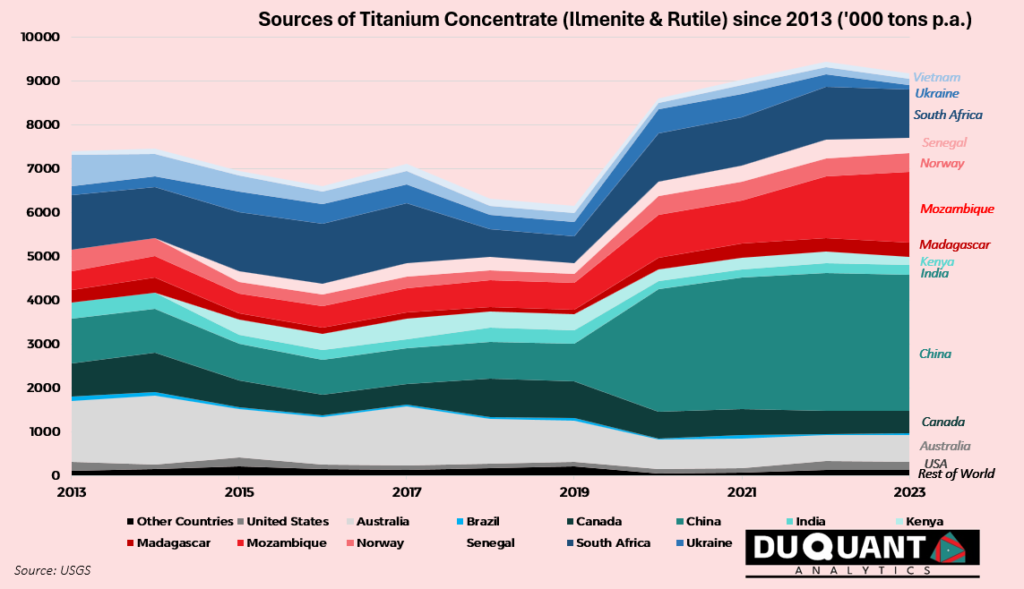
Once titanium dioxide (TiO₂) is isolated from titanium concentrates, the processes to produce titanium pigment and titanium sponge differ significantly, as they are designed to yield products for vastly different applications. A staggering 90-95% of titanium dioxide goes to producing titanium pigment for the use in whitening, with vast applications in paints, coatings, plastics, paper, and other products. TiO₂’s brightness, whiteness, and opacity are highly valued for these use cases. The remaining titanium dioxide is used for sponge, and eventually metal where its use cases are also vast in the aerospace and transportation sectors.
Titanium pigment: is produced by refining the TiO₂ and enhancing its purity, brightness, and opacity for use in products like paints, plastics, and cosmetics. Globally the largest producer of titanium pigment is China (56% of global production & refining capacity), followed by USA (14%), Germany (4%), Mexico (4%), Australia (3%) and Japan (3%). The remainder of the world is ~16%.
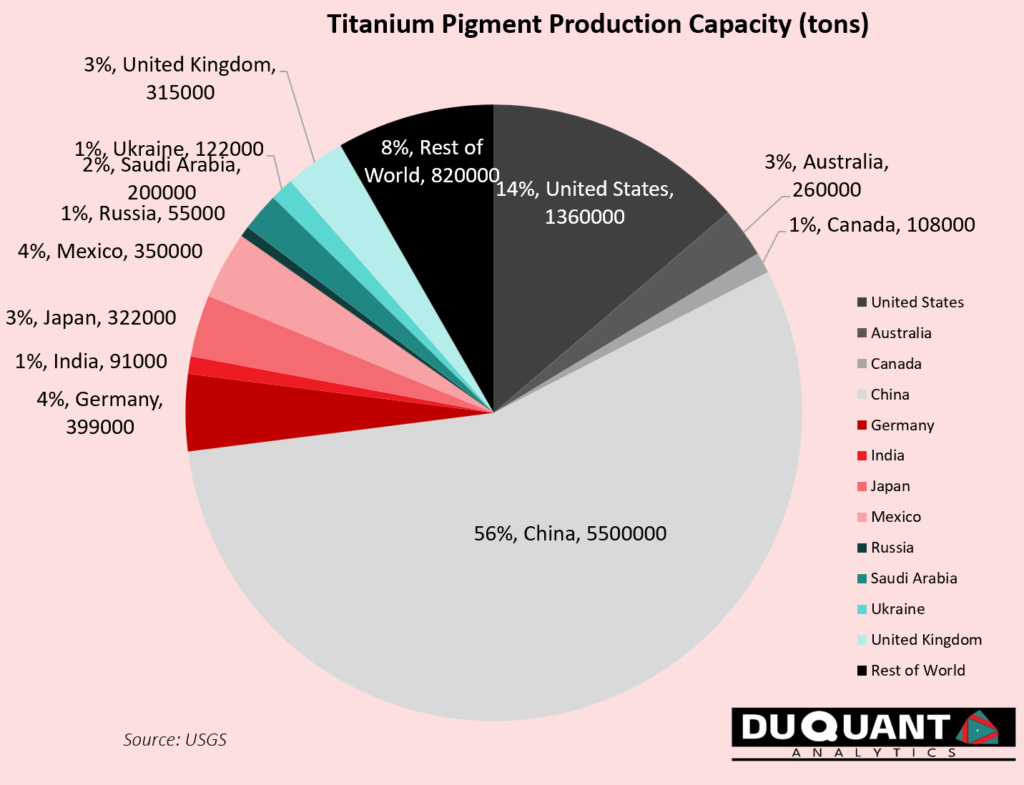
Titanium sponge: The concentrated titanium ore undergoes chlorination to produce titanium tetrachloride (TiCl₄). This is done in a high-temperature reactor where the concentrate is mixed with chlorine and a reducing agent, usually carbon. The Titanium Tetrachloride is then reduced in the Kroll process, where it reacts with magnesium at high temperatures in an inert atmosphere, creating porous titanium metal known as “sponge.” Bulk raw titanium sponge is typically what is commonly traded in commodity markets.
The titanium sponge undergoes further refining, with impurities removed, to reach high purity. It’s then melted into ingots or forged into shapes for specific applications, such as in the aerospace, medical, energy and industrial applications due to its high strength-to-weight ratio and resistance to corrosion.
Globally, the largest production capacity for titanium sponge is China, making up 260kt of capacity (62.8% of world), followed by Japan (15.7%), Russia (11.2%, Kazakhstan (6.3%), and Saudi Arabia (3.8%).
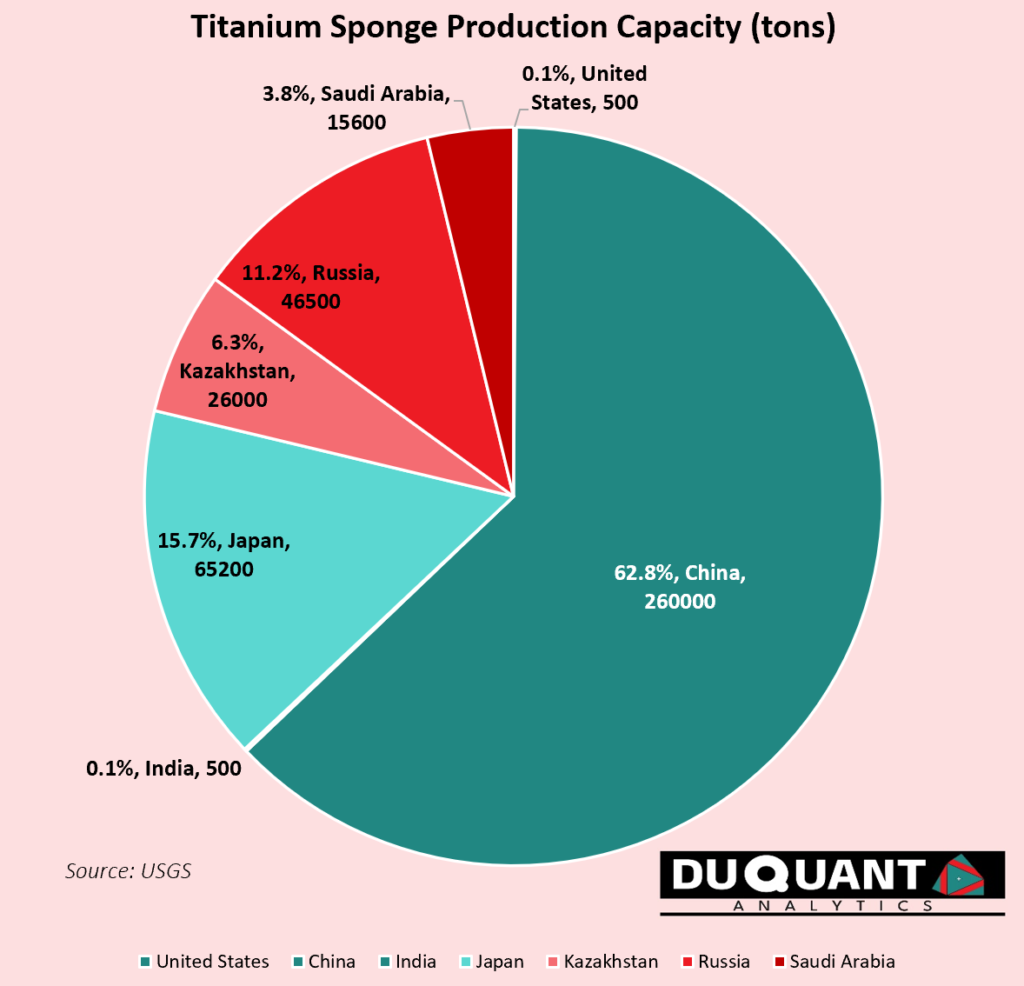
It is interesting to note that while Russia makes up 11.2% of titanium sponge capacity, they do not contribute in terms of raw mined titanium concentrates, – highlighting the complexity of the entire supply chain, from ore to refining and multiple steps and players involved in producing refined titanium metal.
The Remarkable History of Titanium
Titanium, a remarkable metal known for its strength, light weight, and resistance to corrosion, has an intriguing history that spans centuries. Its journey from discovery to becoming a critical material in aerospace, medical, and industrial applications is a testament to the power of scientific innovation and technological advancement. This narrative highlights key events and discoveries that have shaped the titanium industry over time.
The story of titanium begins in the late 18th century. In 1791, Reverend William Gregor, an amateur geologist in England, discovered a new mineral in a local stream. This mineral, later named menachanite (now known as ilmenite), contained an unknown metal. Four years later, in 1795, the German chemist Martin Heinrich Klaproth independently discovered the same metal in a different mineral, rutile. Klaproth named this new element “titanium” after the Titans of Greek mythology, recognizing its strength and durability.
Throughout the 19th century, scientists made significant strides in understanding and isolating titanium. However, it was not until 1910 that Matthew A. Hunter, an American metallurgist, successfully produced pure titanium metal. Using a process that involved heating titanium tetrachloride with sodium in a sealed steel tube, Hunter’s method, known as the Hunter process, marked a major breakthrough in titanium metallurgy.
The early 20th century saw the first significant industrial applications of titanium. During World War II, researchers in the United States and the Soviet Union began exploring titanium’s potential for military applications due to its high strength-to-weight ratio and resistance to corrosion. This interest led to the development of more efficient production methods.
In 1940, William J. Kroll, a Luxembourgish metallurgist, developed a more economical and efficient method for producing titanium metal. The Kroll process, which involves reducing titanium tetrachloride with magnesium, became the dominant method for titanium production and is still used today. This process significantly lowered the cost of titanium production, making it feasible for widespread industrial use.
The mid-20th century marked a turning point in the utilization of titanium, particularly in the aerospace industry. Titanium’s unique properties made it ideal for aircraft and spacecraft components, where strength, light weight, and corrosion resistance are critical.
1950s: Titanium in Jet Engines and Airframes
During the 1950s, titanium began to be used extensively in military and commercial jet engines and airframes. The U.S. military, in particular, invested heavily in titanium for its high-performance aircraft, including the iconic Lockheed SR-71 Blackbird, which featured a titanium structure to withstand extreme speeds and temperatures. This period also saw the development of titanium alloys, which further enhanced the metal’s properties for aerospace applications.
1960s: Expansion into Space Exploration
The 1960s saw titanium’s role expand into space exploration. NASA utilized titanium in various components of its spacecraft due to its excellent performance in the harsh conditions of space. The Apollo Lunar Module, which successfully landed humans on the moon in 1969, incorporated titanium parts to ensure reliability and safety.
As the titanium industry grew, so did concerns about its environmental impact. The extraction and processing of titanium ore generate waste materials and emissions. In response, the industry has increasingly focused on sustainable practices, including the recycling of titanium scrap and the development of more environmentally friendly production methods.
The Late 20th and Early 21st Centuries: Diversification and Innovation
The late 20th and early 21st centuries saw titanium’s applications diversify beyond aerospace into various other industries. Titanium’s biocompatibility, meaning it does not cause adverse reactions when in contact with human tissue, made it invaluable for medical applications. In the 1970s and 1980s, titanium became the material of choice for surgical implants, such as hip and knee replacements, as well as dental implants. Its strength, light weight, and resistance to bodily fluids ensured long-lasting and successful medical devices. The unique properties of titanium also led to its use in a range of industrial and consumer products. Titanium dioxide, a white pigment, became widely used in paints, coatings, and cosmetics due to its brightness and opacity. Additionally, titanium’s corrosion resistance made it ideal for chemical processing equipment, marine applications, and even sporting goods like golf clubs and bicycles.
The 21st century has seen significant advances in titanium manufacturing, particularly in the field of additive manufacturing (3D printing). Titanium’s ability to be precisely shaped through 3D printing has opened up new possibilities for complex and customized components in aerospace, medical, and industrial applications. The 2010s marked a growing demand for lightweight, high-performance materials across various industries. In the automotive sector, manufacturers began incorporating titanium to reduce vehicle weight and improve fuel efficiency. The demand for titanium in consumer electronics also increased, with the metal being used in sleek, durable designs for smartphones, laptops, and wearable devices.
The 2020s have been characterized by a heightened focus on sustainability and recycling in the titanium industry. Innovations in recycling technology have made it possible to recover high-purity titanium from end-of-life products, reducing the need for primary mining and minimizing environmental impact. Additionally, efforts to improve the energy efficiency of titanium production processes continue to gain momentum.
As technology continues to advance, titanium’s importance is set to grow. The metal’s unique combination of strength, light weight, and corrosion resistance makes it essential for the development of next-generation aerospace, medical, and industrial technologies. Research and development efforts are focused on enhancing titanium alloys, improving recycling methods, and finding new applications for titanium in emerging fields such as clean energy and advanced manufacturing.
From its early use in alloys and pigments to its central role in aerospace and medical applications, the journey of titanium is a testament to its enduring value and versatility. Its story reflects the dynamic interplay between natural resources and technological advancements, shaping the future of our high-tech and sustainable world.
Navigating Titanium
Navigating Titanium Titanium has a remarkably high strength-to-weight ratio and corrosion resistance, which is why…